Understanding the Basics of Welding Inspection to Make Sure Top Quality and Security
In the world of contemporary engineering, welding inspection stands as a keystone for guaranteeing both the top quality and safety of structural creations. The procedure includes a thorough analysis of welded joints, utilizing innovative techniques such as ultrasonic and radiographic testing to identify concealed blemishes. The knowledge of licensed assessors is critical, as they connect the gap in between theoretical standards and practical application. Their role expands past plain discovery, including the documentation and communication of findings to relevant stakeholders. Yet, what are the subtleties of these assessment techniques that make them important for maintaining architectural stability?
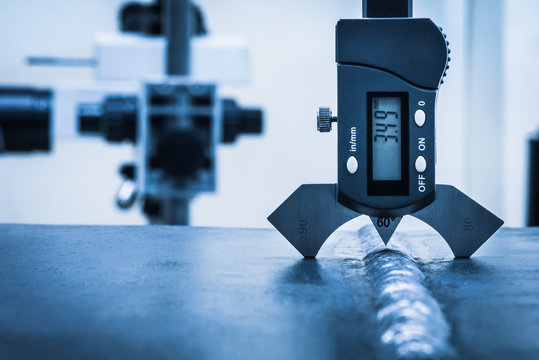
Significance of Welding Inspection
In the realm of commercial construction, the importance of welding inspection can not be overstated. Welding assessment plays a crucial duty in guaranteeing the integrity, safety, and durability of bonded structures. Given the diverse applications of welding in sectors such as building and construction, vehicle, aerospace, and shipbuilding, the requirement for strict quality assurance actions is extremely important. Proper examination makes certain that welds fulfill defined codes and standards, which is important for protecting against architectural failings that can cause disastrous consequences.
The process of welding naturally includes complex variables, including temperature, product properties, and ecological problems, every one of which can affect the quality of the weld. A comprehensive examination determines issues such as cracks, porosity, and incomplete combination, which can jeopardize the toughness and reliability of the weld. By detecting these issues early, corrective actions can be taken, thus lowering the danger of failure and linked costs.
Furthermore, welding evaluation adds to regulative compliance, as several sectors are governed by strict safety and security requirements and guidelines. Failure to abide by these policies can lead to economic penalties and legal responsibilities. Eventually, welding inspection not just safeguards physical structures yet also protects human lives and supports industry online reputations.

Secret Welding Evaluation Methods
Although welding evaluation is vital to making sure the top quality and safety and security of welded structures, it is the details techniques employed that figure out the performance of the inspection process. Key welding examination approaches can be broadly categorized right into non-destructive testing (NDT) and destructive screening. Non-destructive testing approaches such as aesthetic assessment, ultrasonic testing, radiographic screening, magnetic bit screening, and fluid penetrant testing are largely made use of to evaluate the buildings of a weld without creating damage. Visual assessment is usually the initial action, including a thorough evaluation of the weld's surface area for flaws like cracks or porosity.
Ultrasonic and radiographic screening are a lot more innovative methods that enable inspectors to analyze the inner integrity of the weld. Ultrasonic testing makes use of high-frequency sound waves to identify discontinuities, while radiographic testing uses X-rays or gamma rays to produce a picture of the weld's interior. Magnetic fragment screening and liquid penetrant testing are surface examination approaches made use of to locate surface and near-surface problems. On the other hand, damaging testing techniques involve literally damaging or cutting the weld to assess its mechanical homes. These extensive examination methods make certain that welds satisfy market criteria and safety needs, therefore ensuring architectural honesty and efficiency.
Function of Certified Inspectors
Qualified inspectors play a pivotal function in the welding inspection process, ensuring that all welds follow rigid sector standards and safety and security laws. Their proficiency is important in determining issues or irregularities that might jeopardize the architectural stability of a weld. By diligently analyzing each weld, accredited assessors help protect against potential failures that can lead to unsafe mishaps or costly repair work.
To come to be certified, examiners need to go through strenuous training and testing, which acquaints them with different welding strategies, materials, and testing approaches. This detailed knowledge allows them to assess weld high quality successfully and make informed judgments concerning their security and dependability. Certified assessors are proficient in analyzing blueprints and requirements, making sure that the welding work straightens with the project's layout demands.
An indispensable component of their duty is to record their searchings for thoroughly, giving a detailed record of the examination procedure. This documentation is important for traceability and liability, offering as an official document of conformity with sector requirements. Licensed inspectors additionally play an essential function in facilitating interaction in between project stakeholders, offering insights and suggestions to improve welding methods and results. Their contribution is essential in preserving high degrees of quality and safety and security in welding procedures.
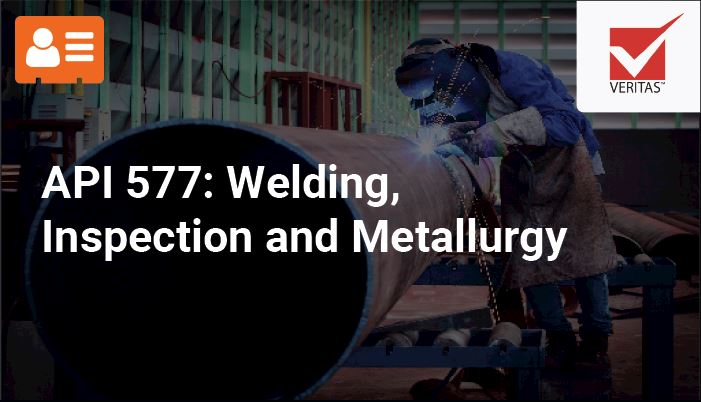
Tools Made Use Of in Welding Inspection
Welding inspectors depend on a variety of specialized devices to perform their tasks effectively, making sure each weld satisfies the essential standards. Amongst these devices, visual assessment help like multiplying glasses and mirrors are essential, permitting inspectors to carefully take a look at welds for surface flaws such as fractures, porosity, and undercut. Calipers and fillet weld gauges are vital for gauging weld dimensions to confirm conformity with layout specifications.
Advanced devices expand beyond visual aids, consisting of non-destructive screening (NDT) tools. Ultrasonic screening gadgets are critical in identifying subsurface flaws, utilizing audio waves to expose internal discontinuities without compromising the weld's integrity. Likewise, radiographic screening uses X-rays or gamma rays to capture photos of a weld's inside, highlighting possible flaws.
Magnetic bit testing is another crucial more device, especially for discovering surface area and near-surface suspensions in ferromagnetic products. By applying ferrous bits and magnetic areas, inspectors can determine problems that might otherwise be undetectable.
Dye penetrant examination is typically made use of for non-ferrous materials, supplying a contrast-enhanced click to investigate aesthetic look for surface-breaking defects. Welding Inspection Madison. With each other, these devices enable welding assessors to adequately assess weld quality, making sure security and reliability in numerous applications across industries
Guaranteeing Structural Stability

Welding treatments should follow well established standards and codes, such as those defined by the American Welding Society (AWS) or the International Organization for Standardization (ISO) These standards ensure that the welds can stand up to operational anxieties and ecological variables. Qualified and licensed welders play a critical function in this procedure, as their competence makes certain that methods are used appropriately, lessening issues such as splits, porosity, and insufficient blend.
Post-weld examination is one more crucial part of confirming structural integrity. Non-destructive screening (NDT) methods, including ultrasonic testing and radiographic testing, are employed to discover subsurface problems without endangering the welded framework. These inspections validate that the welds fulfill the required quality criteria, giving guarantee of their resilience and dependability. Ultimately, ensuring structural honesty in welding not only safeguards human lives yet also protects financial investments and boosts the long life of engineered frameworks.
Conclusion
The principles of welding informative post evaluation are essential for keeping the high quality and safety of bonded structures. The use of specialized devices even more improves the inspection procedure, eventually protecting human lives and lengthening the life expectancy of welded constructions.
Welding inspection plays an essential function in ensuring the honesty, safety and security, and durability of bonded frameworks.Although welding inspection is essential to guaranteeing the high quality and security of welded structures, it is the specific methods utilized that identify the effectiveness of the inspection process. Key welding inspection methods can be extensively categorized right into non-destructive screening (NDT) and devastating testing.Qualified examiners play an essential function in the welding assessment process, ensuring that all welds abide with stringent industry requirements and security guidelines.The principles of welding inspection are crucial for keeping the quality and security of bonded frameworks.